Leading Refractory Company in Malaysia: Expert Solutions
Our management, supervision and crews are highly experienced in the latest refractory materials and installation procedures.
All refractory crews are well trained and equipped with NIOSH Confined Space training enabling us to penetrate into stringent industry such as Petrochemical and Oil & Gas. The crews have undergone strict training and qualification test base on API 936 requirements.
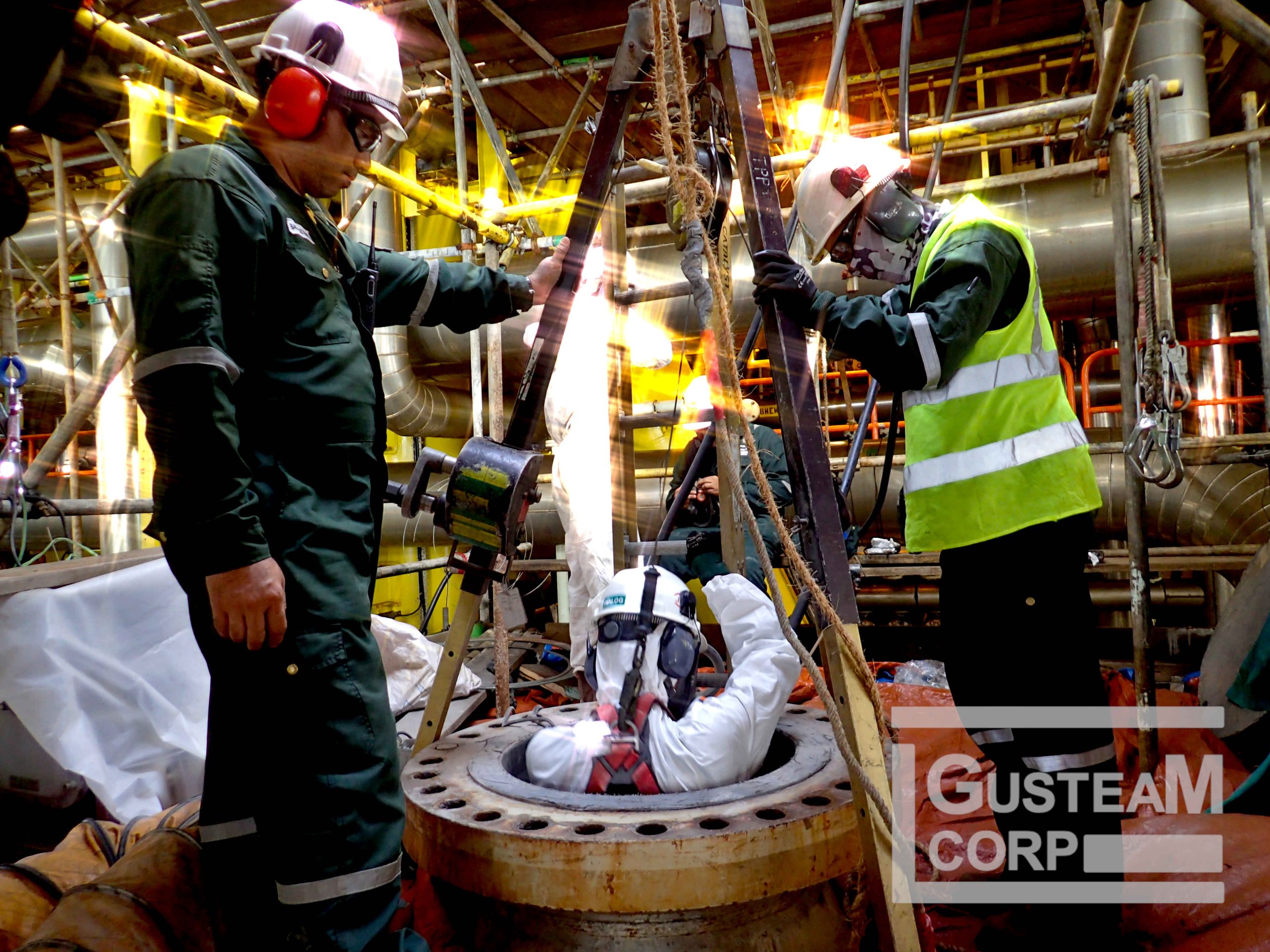
Our capabilities include:
Ceramic Fiber Lining
Ceramic fiber linings are lightweight, energy-efficient solutions designed for high-temperature processes. Compared to traditional monolithic and brick linings, ceramic fiber linings are easier to install, reducing installation costs and eliminating the need for a time-consuming dryout process.
However, these linings are not ideal for high-velocity processes due to their fibrous nature. Another crucial consideration is the anchoring system, as many failures occur from improper anchor welds or the use of incorrect anchor.
For expert guidance and tailored solutions, feel free to contact us. We’re here to assist with all your refractory lining needs.
Monolithics Lining
Guniting, Ramming, Casting
Monolithic linings are widely used across industries such as steel, cement, petrochemical, and waste disposal due to their versatility. Available in various forms with diverse chemical and physical properties, these linings can be tailored to meet the specific requirements of different processes. Key features include durability, chemical inertness, high-temperature thermal shock resistance, and abrasion resistance.
However, proper installation, curing, and dryout are critical to ensuring optimal performance. Following the material manufacturer’s installation guidelines is essential to allow the lining to develop its intended chemical and physical properties. Neglecting these steps may compromise the lining’s effectiveness and durability.
For more information or expert assistance, feel free to contact us. We’re here to support your industrial needs.
Abrasion Resistant Lining
Abrasion-resistant linings are essential for protecting equipment and structures exposed to moderate or extreme sliding wear and abrasion. These linings are designed to withstand the abrasive effects of chemical or mechanical processes, helping to prevent erosion, corrosion, and chemical attacks. By reducing damage, they significantly extend the operational life of equipment and structures.
Choosing the right lining material and understanding the expected costs are key to achieving long-lasting and cost-effective abrasion protection. For tailored solutions and expert advice, feel free to contact us. We’re here to assist with your needs!
Brick Lining
Brick linings are highly valued for their ability to withstand high temperatures, offer low thermal conductivity, and provide excellent energy efficiency. Traditionally used in furnaces, kilns, and fireboxes, brick linings are also chemical-resistant, making them ideal for harsh environments such as storage tanks, pickling tanks, and fertilizer silos.
Unlike monolithic linings, the chemical and physical properties of brick linings are established during production, ensuring consistent structural integrity throughout the lining. Additionally, brick linings do not require a dryout process, as the bricks are pre-dried during manufacturing.
For guidance on selecting the right type of brick lining for your specific requirements, feel free to contact us. We’re here to assist with tailored solutions for your industrial needs!
Special Shapes
Special shapes refractory blocks or bricks are custom-designed to fit unique equipment configurations, ensuring optimal performance in regulated and controlled environments. Like standard bricks, their structural properties are precisely defined during production and dried before shipment, ensuring consistency and reliability.
If you require custom-made refractory shapes tailored to your specific lining needs, feel free to contact us. We’re here to provide expert solutions for your unique applications!
Dry out for both localised electrical and gas burner for wide areas.
A proper refractory dryout is as crucial as ensuring the refractory cures correctly. Skipping or improperly conducting the dryout process can result in thermal spalling or, in severe cases, a dangerous steam explosion that may destroy the entire lining.
Refractory dryout is a controlled process where heat is applied at precise rates to remove retained free and chemical water from the lining. Depending on the area, this can be achieved using electrical heating for localized repairs or gas burners for larger sections.
For professional guidance and assistance with your refractory dryout process, feel free to contact us. Safety and durability start with proper procedures!